Updated: August 22, 2025
Written by Dan Simms
Laura Madrigal is the Home Design Specialist at Fixr.com, dedicated to identifying and analyzing significant changes within residential design. She is the author of leading trends reports on interior design, kitchen, and bathroom, and her insights have been featured in publications like Realtor and the New York Post.
Learn moreReviewed by Laura Madrigal
When it’s time to replace your roof, asphalt shingles are probably the first material that comes to mind, but metal roofing is a great alternative that can provide even more value over time. Metal roofing is recyclable and more sustainable than other materials; it lasts twice as long, stands up better to impact and high winds, and it excels in most climates, shedding snow more readily in cold, snowy areas and reflecting sun to improve your home’s energy efficiency in hot, sunny climates. The durability and low maintenance of a metal roof are key reasons for its popularity.
The average installation cost of a 2,400 sq.ft. steel roof is $26,500, with typical costs falling somewhere between $14,400 and $38,400. There are many different factors that can affect material costs and labor costs, including the roof size, the size of your home, the type of roof you choose, the style of roof you want, the design and complexity of your roof, and more. To make an informed decision about your new roof, it's essential to understand all these factors.
Cost of Metal Roof
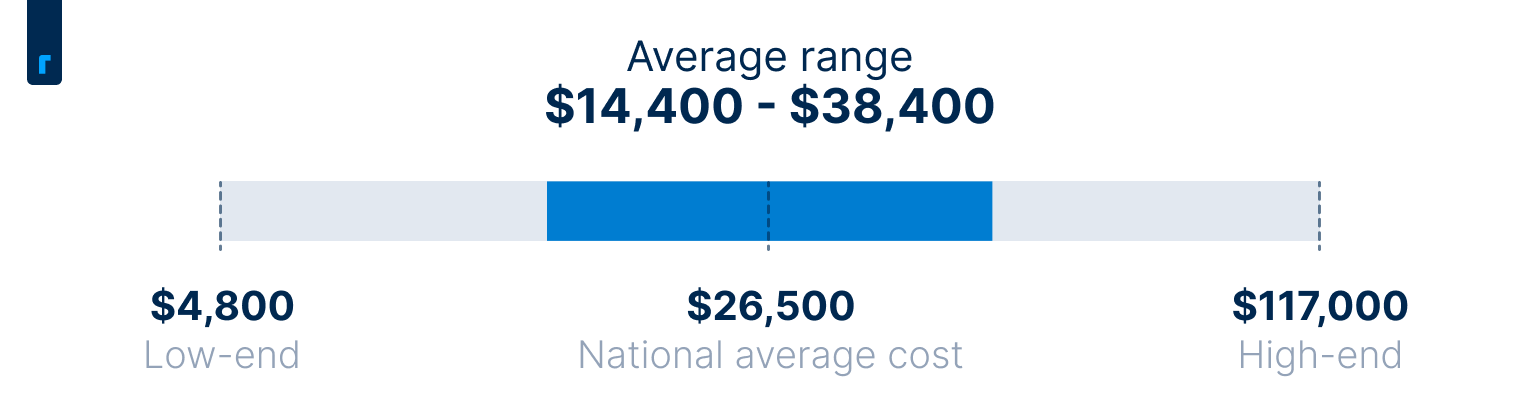
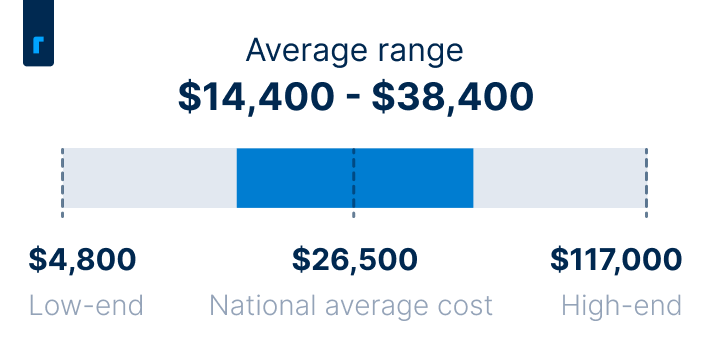
Metal Roof Cost per Square Foot
Metal roof installation costs an average of $11 per square foot, including materials and labor. Your cost per square foot can range from $3 to $30 per square foot, mostly depending on the type of metal and the style of metal roof you choose.
When estimating metal roof prices, it’s a good idea to start with a per-square-foot cost and then apply that to your specific home. You can use roofing calculators to determine how many square feet of roofing you need. Just remember that roof square footage is often higher than home square footage, as it must account for roof overhang and slope. For example, a 1,000-square-foot home needs an average of 1,200 square feet of roofing, and a 2,000-square-foot home needs 2,400 to 2,500 square feet of roofing.
Metal Roofing Cost by Material
The type of metal you choose for your new roof will have a major impact on your total costs. Steel roofs are the most popular option, but aluminum and tin are more cost-effective, and zinc and copper roofing create a more unique look for your home. The price range varies widely by material, ranging from $3 to $30 per square foot, including installation.

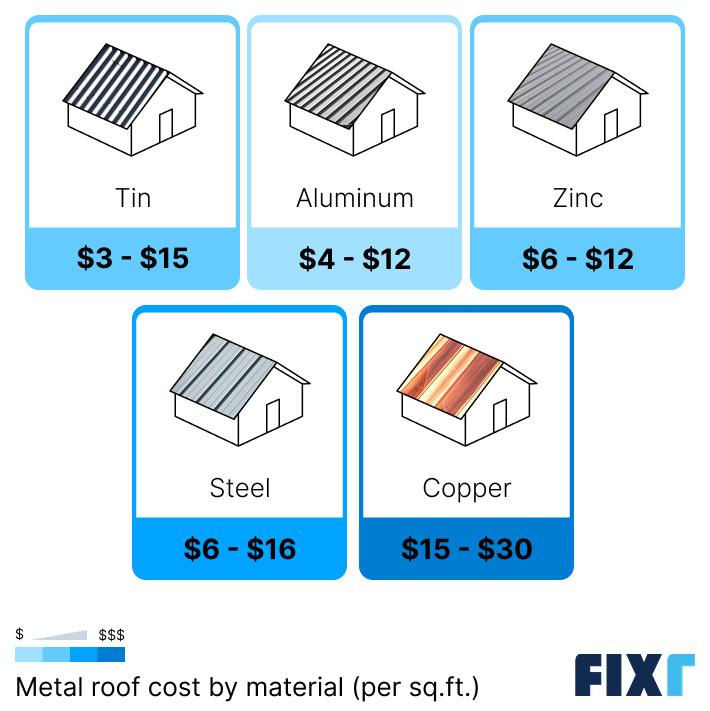
Material | Cost per sq.ft. |
$3 - $15 | |
$4 - $12 | |
Zinc | $6 - $12 |
Steel | $6 - $16 |
$15 - $30 |
Tin
Tin is the most affordable metal roofing material to install, with materials and labor totaling between $3 and $15 per square foot. Tin roofs can last for up to 70 years, so while the upfront cost is low, the material still provides outstanding value.
While tin won’t rust, it is softer than aluminum, so it’s more likely to dent from hail or blown debris and may not be ideal in areas that see extreme weather conditions. It also expands and contracts more than other metal options, so fasteners can loosen, leading to more maintenance and a higher risk of leaks. You can choose to paint or powder coat your tin roof for added protection and customizability.
Aluminum
Aluminum roofing is an affordable roofing solution, costing between $4 and $12 per square foot for materials and installation labor. Aluminum is a softer metal, so it won’t handle impact as well as some other metal options, but it’s still more resistant to puncture than asphalt shingles. Aluminum can be painted or powder coated for customizability
Aluminum doesn’t rust, which can lead to less maintenance for safety purposes. However, it’s more likely to dent from hail or blown debris, so you may need minor dent repair more often. Aluminum’s rust-proof nature makes it a good option in coastal areas, where salty air can speed up corrosion of other materials.
Zinc
Zinc roofing costs between $6 and $12 per square foot, including materials and labor. While it's generally more affordable than some premium metals, zinc can outlast many other roofing materials, potentially providing up to 100 years of life. Zinc also boosts home value more than these other options, as it develops a beautiful patina, just like copper, and makes for a unique home appearance.
Much like aluminum, zinc won’t rust, in part because of the protective patina that develops instead of rust, so it’s a suitable option for coastal climates. However, zinc is a very soft metal, so it will dent more easily than steel and aluminum if it suffers from impact.
Steel Roof Cost
Steel roofing costs between $6 and $16 per square foot, including materials and labor, with an average of $11 per square foot. Steel is the most popular metal roofing option, in large part because it’s extremely durable, can stand up to impact, won’t rust, and delivers outstanding value for the money.
Stainless steel roofing can last for up to 60 years, which is more than twice as long of a lifespan as you’d get from asphalt shingles. You can opt for powder-coated or painted stainless steel to customize color, and the material requires low maintenance. Steel roofing is prone to rusting if the coating is compromised, so maintenance will involve routine inspections and roof repairs after impact.
Copper
Copper is, by far, the most expensive type of metal you can choose for your metal roof, costing between $15 and $30 per square foot for materials and installation labor. Copper is a luxury option in both pricing and aesthetics, though, as the metal develops a natural patina that most homeowners find very appealing. Copper will boost home value more than any other metal roofing material.
Copper also has the longest lifespan of any roofing material, easily topping 100 years and sometimes lasting for up to 200 years. The material is relatively soft, though, so you may need ongoing maintenance and dent repair if you live in a more extreme climate.
Metal Roof Cost by Style
In addition to the type of metal, you have some options for the style of metal roof you install. Standing seam metal roofs cost the most but are also the most common. They total between $7 and $30 per square foot, depending on the specific material. Standing seam metal roofs have hidden fasteners and few seams that make them more resistant to leaks and uplift in strong winds.
Corrugated metal is often the most affordable style, costing as little as $3.50 per square foot, but visually, it’s the least appealing. As a result, most homeowners use this style on outbuildings like sheds and detached garages rather than their main homes. Corrugated metal also has exposed fasteners that detract from the appearance and increase the risk of water intrusion over time.
Metal shingle roofs cost between $6 and $22 per square foot, putting them in the middle in terms of the cost. The materials are more affordable, but the labor costs are higher and mostly make up for the lower material prices. Shingles offer good leak protection, as they also have hidden fasteners, but they’re more prone to uplift and aren’t ideal in areas that see frequent heavy winds from tornadoes, hurricanes, or tropical storms.
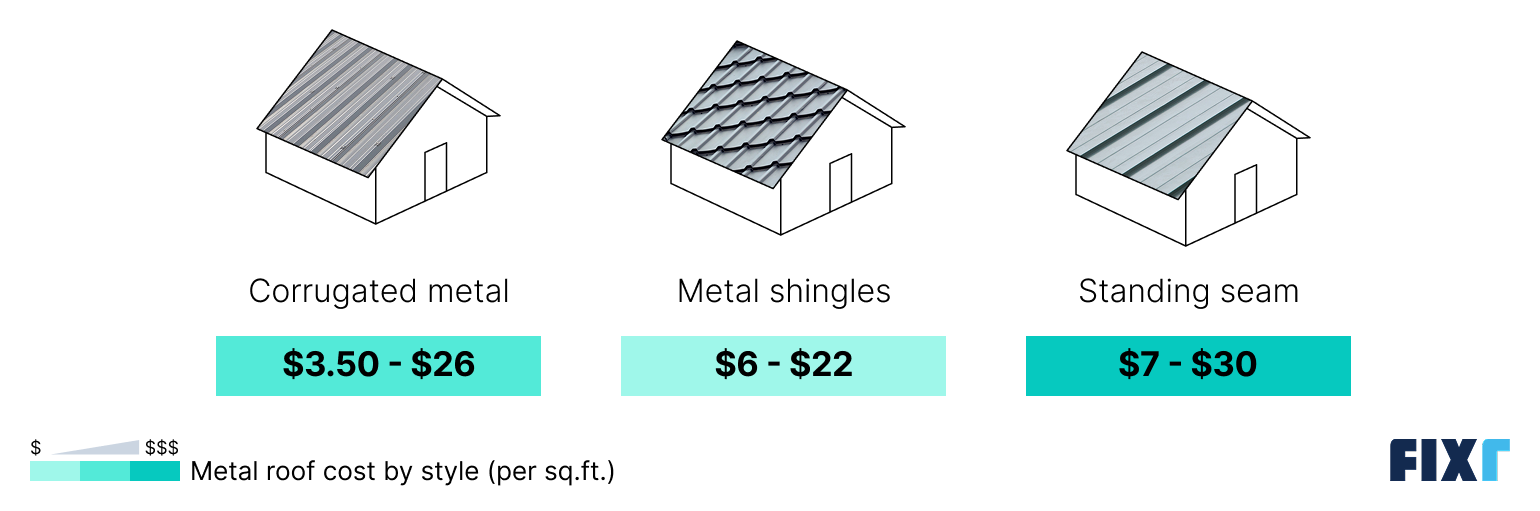
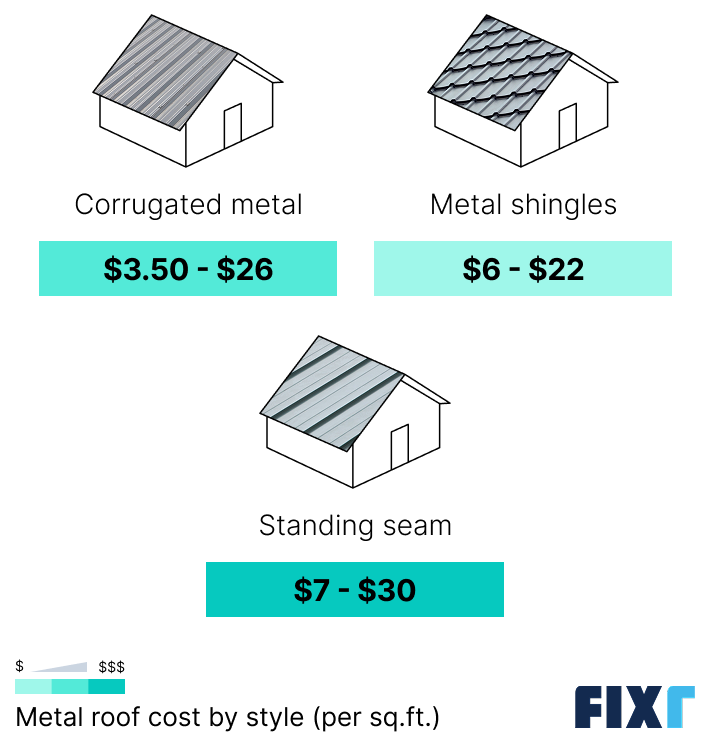
Type | Cost per sq.ft. |
Corrugated metal | $3.50 - $26 |
Metal shingles | $6 - $22 |
Standing seam | $7 - $30 |
Metal Roof Replacement Cost by House Size
Like all roof materials, your roofer will price out your metal roof installation based largely on the square feet of roofing you need, and both materials and labor will scale with roof square footage. Larger roofs require more materials and will take longer to cover. Roofers may loosely charge based on a specific cost per square foot, but since roofs vary so widely in design and complexity, you’ll more likely get just a total for your roofing project rather than a breakdown by size.
You can get the most accurate estimate if you know how many square feet of roofing you need to cover your home. However, more homeowners know their home’s square footage, and while these measurements differ, they are correlated. You can use the table below to get an idea of the average metal roof installation cost based on home size.
House Size | Cost Range |
1,000 sq.ft. | $4,800 - $36,000 |
1,500 sq.ft. | $7,200 - $54,000 |
2,000 sq.ft. | $9,800 - $73,500 |
2,500 sq.ft. | $12,200 - $91,500 |
3,000 sq.ft. | $15,600 - $117,000 |
Labor Cost to Install Metal Roof
The average labor cost to install a metal roof is between $3 and $12 per square foot, with an average of $6.50. The average metal roofing labor cost per square is between $300 and $1,200. Labor typically accounts for between 50% and 80% of your total, with an average around 60%. The percentage for labor can be as low as 25% when you choose luxury materials, like copper.
Labor costs vary so much because of the wide range of material costs for different metal types and roof styles, variable installation complexity due to different roof shapes and designs, and more.
Additional Factors Affecting the Cost of Metal Roofing
The type of metal roof you choose and the style are the two biggest cost factors you need to consider, but there are a handful of other additional costs to consider if you want the most accurate estimate possible.
Gauge of Metal
Unlike most other roofing materials, metal roofs come in varying thicknesses. Thicker metal panels or shingles will resist denting better, making them better options in areas that see extreme weather. However, opting for thicker metal also drives up your material costs and may make installation a bit more challenging.
Metal roofs for residential use are usually available in gauges ranging from 22 gauge to 29 gauge, with lower gauge numbers representing thicker, more durable, and more expensive products.
Coating or Paint
Unless you’re installing copper or zinc roofing for the natural patina, you’ll most likely want your metal roof powder coated or painted. This improves the curb appeal, but it can drive up costs, especially if you go with a custom color. The quality of the coating or paint will also affect the upfront cost, but can dictate the longevity of the coating, too.
A strong coating is especially important on steel roofs, which are the most common, as the metal can rust over time if left exposed to the elements.
Roof Pitch and Complexity
The pitch of your roof plays an important role in your material and labor costs, as steeper roofs require more roofing material for coverage over a given interior square footage, and slopes over 6/12 often require scaffolding and additional safety equipment that slows down the installation and drives up labor costs. This is a crucial factor to keep in mind, as metal roofing systems are especially popular in areas that see heavy snowfall, and homes in these areas are often designed with particularly steep roofs to help shed snow more easily.
The complexity of your roof also matters, as hips, valleys, and additional gables all require additional flashing, which increases material costs and takes longer to cover, adding to labor costs as well. A simple shed-style roof or gable roof will be the most affordable styles for metal roof installation, while hip roofs, mansard roofs, cross-gables, and dormers can all drive up prices.
Existing Roof Removal
While it’s possible to install a metal roof over existing shingles, it’s usually best to rip the old roof off and start fresh, especially since this can expose any hidden damage that may need to be addressed. You can expect to pay between $1,000 and $7,400 to remove your old roof, depending on the size and the weight of the old materials. Slate and clay roofs can push toward the higher cost of that range, while removing an asphalt shingle roof usually costs between $1,000 and $2,000.
Underlayment
All roofing materials need some type of underlayment for added protection from the elements. Most roofers will include the cost of underlayment in their totals, but some may charge separately for it. There are different underlayment options for metal roofing that range from $0.05 up to around $0.50 per square foot, including materials and labor. Ask your roofing contractor which type of underlayment is right for your climate.
Is Metal Roofing Worth It?
Metal roof installation costs two to three times as much as an asphalt shingle roof, so upfront cost and long-term value are crucial factors to consider when considering a metal roof. While they are more expensive, they last at least twice as long as asphalt shingle roofs, and in many cases, they can last three to four times as long, or more.
You’ll get about the same value or better in terms of longevity as it relates to upfront pricing, but a metal roof is worth the investment because it requires less maintenance, offers better protection against leaks and wind uplift, and can boost energy efficiency and provide savings on cooling bills, especially in hot, sunny climates. Overall, you’ll pay more for a metal roof, but you’ll usually get more value in the long run than you would from a less durable asphalt shingle roof.
Metal vs. Asphalt Roof Cost
Metal roofs average $11 per square foot to install, while asphalt shingle roofs average $4 per square foot. Metal roofs are significantly more expensive, but they require virtually no maintenance and provide better protection from potentially expensive roof leaks. Many homeowners also prefer the look of metal roofing, although the ROI for asphalt shingle roofs tends to be higher due to lower installation costs.
The lower cost and greater ROI on asphalt shingle roofs makes them a far more popular option, but homeowners who live in hot, sunny climates or in areas that see excessive snowfall can easily justify the added cost of a metal roof, as it helps improve home energy efficiency and sheds snow more easily, reducing the risk of structural damage from accumulation.
DIY vs. Professional Installation
With an average of between 50% and 60% of your total metal roof installation costs going toward labor, DIYing often seems like a good option. While it will save you an average of around $13,500, it’s most definitely not worth it in the long run.
Moving heavy materials and maneuvering them around on your roof is always dangerous, so hiring a professional is best to keep yourself safe. Metal roofs can be particularly slick and increase the risk of falls, especially if you have a steep roof designed to help the metal shed snow.
Even if you feel comfortable doing the work, a DIY installation will void most manufacturers’ warranties, and any mistakes you make can lead to expensive water damage that can eat away at the initial savings. Many homeowner’s insurance providers also won’t cover damages that result from leaks on a roof you installed yourself. It’s best to leave metal roof installation to a professional for the best appearance, safest installation, and greatest value.
Ways to Save Money on a Metal Roof
Since metal roofs are far more expensive than standard asphalt roofs, and since DIYing isn’t ideal, how can you get a high-quality metal roof without breaking the bank? Luckily, there are several steps you can take to reduce costs.
Choose your materials carefully: Metal roofing materials range from $3 to $30 per square foot, so choosing the right material can mean thousands of dollars in savings. Avoid high-end copper, but choose a material that’s still highly durable, can stand up to severe weather, and offers good longevity for value. Steel is one of the best options overall for balancing cost and value. Think about the gauge you need for your climate, too.
Pick a less expensive style: Steer clear of corrugated metal roofing if you want a good return on investment and curb appeal, but consider more affordable metal shingles over a standing seam metal roof to save some money.
Aim to get the work done during the off-season: Roofers are busiest during the late spring and early summer, so waiting until the fall to replace your roof could mean lower labor costs thanks to decreased demand.
Look for tax credits and rebates: Metal roofing may qualify you for energy efficiency rebates, tax credits, and other incentives, especially if you choose a light colored metal roof, which is considered a “cool roof.” Check the Database of State Incentives for Renewables and Efficiency (DSIRE) for incentives in your area.
Get at least three estimates: Shop around and get at least three estimates for your metal roof installation. Be sure to ask each contractor for a quote for the same metal, roof thickness, and style, and compare them side-by-side to find the best value.
Avoid old roof removal: In some cases, you may be able to save $1,000 to $2,000 or more by installing metal roofing directly over your old roof. This isn’t always allowed by local building code or advisable, but ask your roofer if it’s an option for your particular case.
Understand when you can call on insurance: If your old roof was damaged beyond repair from extreme weather, you may be able to get the cost of a new metal roof partially covered if you open a homeowner’s insurance claim. You’ll need to pay a deductible, but this could mean significantly less money out of your pocket.
FAQs
The average cost to install a metal roof on a 2,000-square-foot house is $26,950. This is based on the typical home of this size requiring 2,450 square feet of roofing for full coverage and on the average cost per square foot of $11. Your total could range from $9,800 to $73,500, depending on the specific materials you choose.
A metal roof can cost anywhere from $3 to $30 per square foot to install, and the average cost of a metal roof is around $11 per square foot. The actual cost will depend on the type of metal, the style of roof, and the roof gauge. You’ll pay closer to the lower end of that range for tin or aluminum, while copper can push your costs up into the higher end.
There are two primary downsides to a metal roof: the upfront cost and the potential for interior noise. First, metal roofs cost two to three times as much as asphalt shingle roofs, and although they provide equal or better value due to a longer lifespan, the higher upfront cost is still a drawback. Metal roofs can also be noisy in heavy rainfall, so you may need to install insulation underneath the metal to dampen sound inside your home.
Metal roofs last an average of 50 to 70 years, so you should expect to have to replace them every 60 years or so. However, the lifespan depends on many factors, including the climate in your area and the type of metal you choose. Metal roofs will tend to last longer in more moderate climates, and certain types of metal roofs, like zinc and copper, can last for 100 years or more, even in more extreme climates.